Professor John Durodola
BSc MSc PhD DIC
Professor in Mechanical Engineering and Mathematical Sciences
School of Engineering, Computing and Mathematics
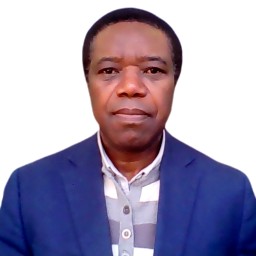
Role
John Durodola is Professor of Mechanical Engineering and teaches modules such as statics and dynamics, stress analysis and strength of components. He is also the Post Graduate Research Tutor for research students in the areas of engineering and mathematics. These modules are studied by BSc, BEng, MEng and MSc students.
Teaching and supervision
Courses
Modules taught
- Introduction to Stress Analysis
- Introduction to Statics and Dynamics
- Basic Stress Analysis
- Advanced Materials and Strength of Components
Research Students
Name | Thesis title | Completed |
---|---|---|
Abhinav Priyardashi | Influence of ultrasonic melt treatment on the fragmentation of primary intermetallics in Al based alloys | 2022 |
Research
My research expertise is in predictive modelling for design of engineering components and mechanical behaviour of materials. I have had the privilege of working with automotive and aerospace companies. My research interests and publications are in the areas of artificial neural networks applied to fatigue and non destructive evaluation (NDE), noise vibration and harshness, light weight vehicle structural analysis, springback during forming processes, functionally graded materials, metal ceramic joining, residual stresses, creep, finite element and boundary element numerical methods and analysis of adhesively bonded structures. i review articles for a number of journals in my field and I am consulted for review of grant applications.
Research grants and awards
- Visiting Fellow - Nanyang University of Technology 2015
- EPSRC Funded NVH Project, £371k, total value £750,000 (2003 – 2007).
- Finite Element Network, European Union, £4,000, 2001-04.
- DoITPOMs HEFCE Funded Dissemination of Information Technology for the Promotion of Materials Science, £7,500, Led by Department of Materials, University of Cambridge, 2001-03.
- Quality Research Funding Grant, Oxford Brookes University, £32,000, 1997- 2000.
- LIVEMAN, EPSRC Funded Adhesive Bonding for Lightweight Vehicle Structures, £181,000, 1997- 2000 (Held with Prof Beveers and Prof Hutchinson).
- Consultant, Structural Materials Centre, Defence Research Agency, Farnborough, 1995.
- Generic Research Funding Grant, £2500, Oxford Brookes University,1994/95.
Research projects
- Visiting Fellow - Nanyang University of Technology 2015
- EPSRC Funded NVH Project, £371k, total value £750,000 (2003 – 2007).
- Finite Element Network, European Union, £4,000, 2001-04.
- DoITPOMs HEFCE Funded Dissemination of Information Technology for the Promotion of Materials Science, £7,500, Led by Department of Materials, University of Cambridge, 2001-03.
- Quality Research Funding Grant, Oxford Brookes University, £32,000, 1997- 2000.
- LIVEMAN, EPSRC Funded Adhesive Bonding for Lightweight Vehicle Structures, £181,000, 1997- 2000
- (Held with Prof Beveers and Prof Hutchinson).
- Consultant, Structural Materials Centre, Defence Research Agency, Farnborough, 1995.
- Generic Research Funding Grant, £2500, Oxford Brookes University,1994/95.
Research impact
My research has influenced work in the reas of functionally graded material, residual stresses, fatigue, creep, adhesive bonded joint analysis, noise vibration harshness, artificial neural network applied to materials.
Groups
Publications
Professional information
Memberships of professional bodies
- Fellow - Institution of Mechanical Engineers (FIMechE)
- Editorial Board – Journal of Mechanical Engineering Science (IMechE Proc C)
- Editorial Board - ISRN Applied Mathematics