PPM offer support and highly qualified services in the following areas:
- CFD and 0D/1D modelling of internal combustion engines
- Development of tailored software and methodologies to support the entire CFD modelling process (from meshing to automatised post-processing)
- Robust methodologies for the calibration of semi-fundamental models
- Spray modelling and spray pattern/targeting optimisation
- Development of tailor-made surrogate fuel blend models
- Combustion modelling including chemical kinetics and soot formation
- Soot mechanisms and interactions in modern high injection pressure Gasoline Direct Injection engines
- Advanced mesh morphing approaches for the simulation of gas and particle dispersion in large urban contexts
- Conjugate heat transfer simulations
- Engine testing, including emission analysis (gas analysers and FTIR) and engine-out Particulate Matter characterisation (DMS-500 by Cambustion)
- Testing of fuels and impact on PM/PN emissions
- Ammonia-hydrogen combustion
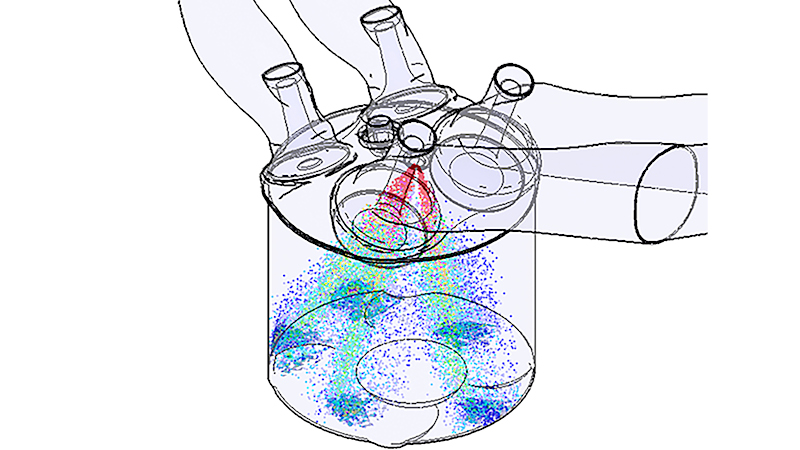