Edward Hopkins
Lecturer in Mechanical Engineering/Research Fellow in Future of Transport
School of Engineering, Computing and Mathematics
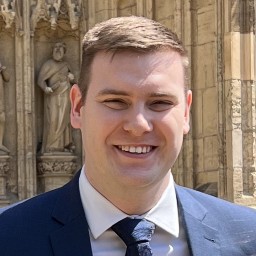
Research
Centres and institutes
Groups
Projects as Co-investigator
- Project Cavendish, Developing zero CO2 hydrogen combustion systems for heavy-duty commercial transport.(01/09/2024 - 28/02/2026), funded by: Technology Strategy Board (Innovate UK), funded by: Technology Strategy Board (Innovate UK)