Dr Neil Fellows
PhD, BEng (Hons), CTHE, CertHE
Reader in Mechanical Engineering
School of Engineering, Computing and Mathematics
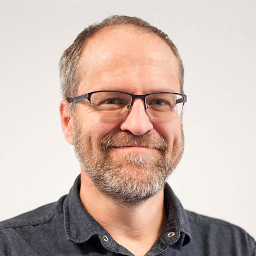
Role
My first degree was in Mechanical Engineering from Salford University. As part of my degree I spent a year working in industry on fluid and hydraulic control systems. My PhD was carried out at Cranfield University where I investigated the high velocity impact on ceramic armour. Following my PhD I took up a post-doctoral position with the University of Oxford, in which I developed methods of recording, photographically, torsional deformation during high speed split hopkison pressure bar tests.
Areas of expertise
- Composite damage modelling
- Low and high temperature behaviour of materials
- Residual stresses generated in components
- due to thermal mismatch
- due to heat treatment
- Thermal flow modelling
- High velocity impact
- Fatigue performance
- metal matrix composites
- aluminium alloys
- adhesive joints
- Autonomous vehicles
- Robot actuator design
Teaching and supervision
Modules taught
- Crash Impact Modelling (MSc/MEng)
- Vehicle Crash Design(MEng/BEng)
- Advanced Stress Analysis (MEng/BEng)
- Stress Analysis and Dynamics (MEng/BEng)
I am also responsible for looking after the placement module. This module provides opportunities for students to do a year long placement as part of their engineering or mathematical science studies. I am also the module leader for the crash and impact modelling courses as well as the advanced stress analysis course.
Supervision
I have supervised ten PhD students to completion. I am currently supervising 6 PhD/Mphil students. I also supervise MSc and MEng projects students.
Research
My research can be summarised as the development and validation of analytical and numerical models for predicting the strength performance of materials and components. My work has focussed on the areas of safety and security.
Research grants and awards
Knowledge Base Supervisor/Lead Academic:
- Development of gas fire suppressant systems for motorsport industry (KTP EOI 2866)
- Development of ground source heat pump collector systems (KTP PN 6548)
Principal Investigator:
- Determination of the mechanical properties of superconducting wires (EPSRC CASE)
- Strain distribution in composite structures at cryogenic temperatures (EPSRC GR/R97344/01)
Investigator:
- Low NVH Multi Material Automotive Vehicle Structures (EPSRC GR/S27245/01)
- LIVEMAN project 3 (EPSRC GR/L03811)
Research projects
- Fracture failure prediction in carbon fuel rods
- Metal Matrix Composite material characterisation
- Development of shape optimization for wind turbine blade
- Modelling Noise and Vibration of an Axial Flux Electrical Motor
- Combustion process in Gasoline Direct Injection Engines for cleaner and Optimum Fuel economy
Research impact
The highlights of my research can be summarised as below:
- Development of a two stage light gas gun facility (velocities up to 3.5km/s) and verified models of high velocity impact of alumina armour.
- Development of a photographic technique to measure shear patterns, enabling high strain rate torsional modelling of REMCO Iron and copper.
- Determination of the effect of adhesive modulus on the torsional stiffness and strength of automotive structures enabling the overall vehicle torsional stiffness to be determined.
- Investigation of NVH in a single composite van roof leading to a new adhesive joint which was easier to implement and had considerable strength and fatigue benefits over existing designs.
- Development of an experimental method to validate models of failure strength in metal to composite aircraft joints, to give a higher confidence in aircraft design practise.
- Development of predictive tools to compensate for springback within forming processes to reduce material waste and time consuming iterative manufacture.
- Validation of simple tests to show their applicability for determining Bauschinger’s effect in metals, reducing the cost of determining this important material parameter.
- Determination of the mechanical properties and residual stresses of superconducting wires and coils (during the heat treatment process and at low temperatures), enabling coil design to be optimised for greater performance.
- Application of an optical method to resolve the controversy about whether crack closure is the main fatigue crack growth mechanism.
- Development of numerical models for designing compact heat pump collectors, enabling smaller plots of land to be used which opens up a larger share of the market for manufacturers.
- Development of analytical models, using neural networks and ultrasound, to carry out quicker and more reliable safety inspection of components.
Groups
Publications
Professional information
Memberships of professional bodies
- Chartered Engineer
- Member of the Institue of Mechanical Engineers
Consultancy
I have carried out consultancy and contract testing in the area of stress analysis for many local and regional companies.
Further details
Reviewer for the:
- International Journal of Impact Engineering
- International Journal of Fatigue
- Engineering Fracture Mechanics
- Structural Engineering and Mechanics